
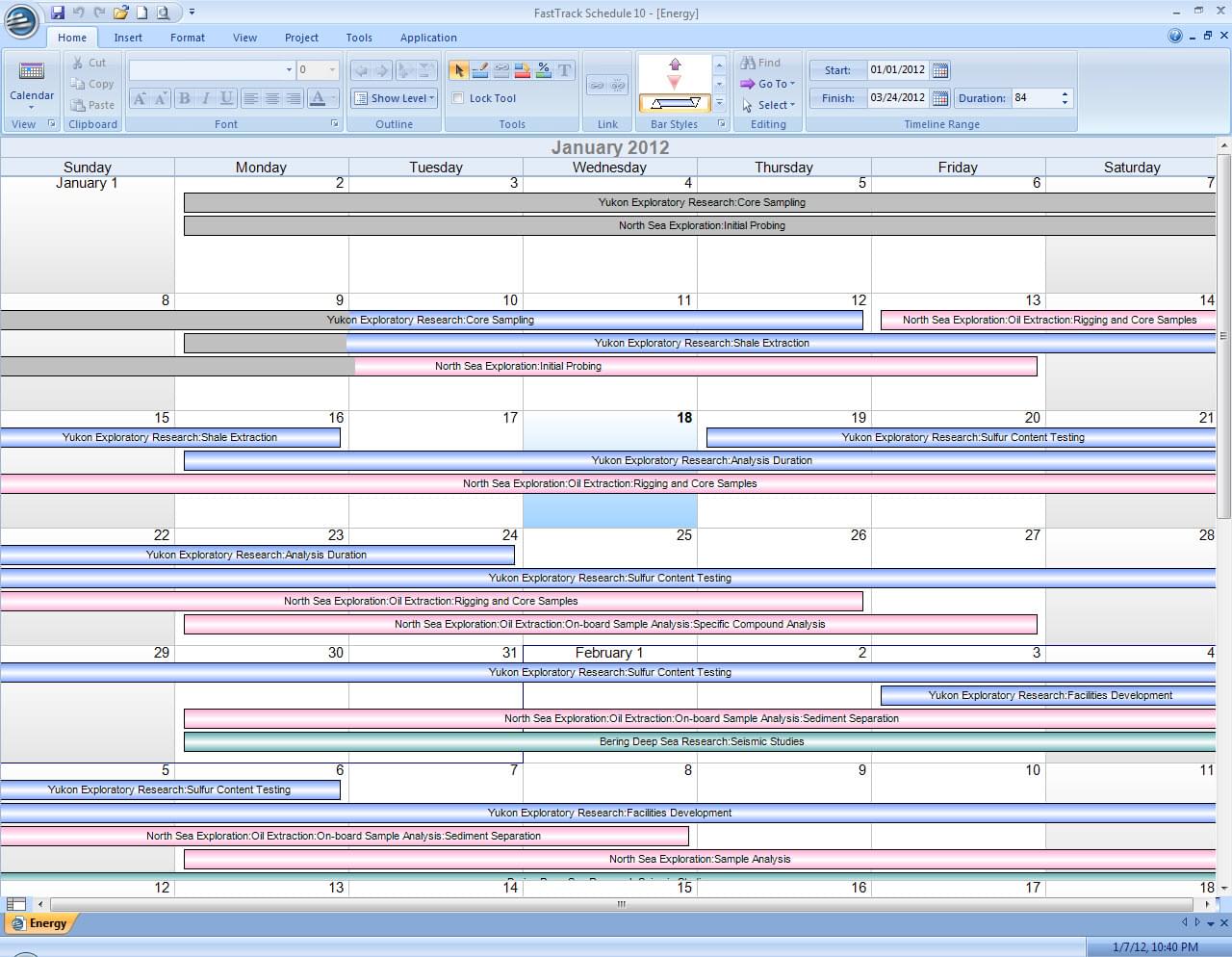
Therefore, the understanding of bolt joint characteristics is essential for improving machine design and assembly. Yuansheng, Li Guangpeng, Zhang Zhen, Zhang Ping, Wangīolt joints are common in machine tools and have a direct impact on the overall performance of the tools. Also, two types of sheets infuence the joint behaviour as the reinforced joints display more ductility behaviour.Ī Modelling Method of Bolt Joints Based on Basic Characteristic Parameters of Joint Surfaces The results show that the reinforced samples have higher tensile strength compared to that of reinforced joints, although it is not statistically signifcant. The tensile strength of the reinforced and control samples (un-reinforced joints was measured according to ASTM D5652-92 standard. Also the effect of adding a wood veneer on the reinforced joints was investigated. They were then kept at room temperature for three weeks. In this respect, one layer of GFRP sheet was used to be bonded to timber members by using epoxy resin and left between the clamps for 24 hours. The employed steel bolt was 10 cm in length and 1 cm in diameter. The thickness of each member was 4 cm for internal part and 2 cm for external part. A single shear bolted joint consisted of 3 timber members whose length and width were 30 cm in length and 5 cm in width. This research aims to study the behaviour of bolted joints in poplar and pine woods, which are reinforced by two types of GFRP sheets.
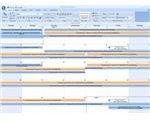
Therefore, the idea of using composite sheets in timber joints has been intro-duced as a method in order to increase the strength and ductility behaviour of timber joints. Reinforcement of Bolted Timber Joints Using GFRP Sheets in Poplar and Pine Woodsįull Text Available Failure in timber structures occurs mainly in crucial points such as joints areas. Higher magnitudes of loads and frequencies are also observed more challenging to the joints performance. The cyclic axial loads are concluded relatively more challenging for both the sealing and strength of the joint. In this study a three dimensional finite element analysis of a gasketed joint is carried out using a spiral wound gasket under bolt up and dynamic operating conditions (internal pressure, axial and bending singly and in combination. Most of the work available in literature is under static loading, whereas in industry, cyclic loads are applied due to the vibrating machinery such as motors, pumps, sloshing in offshore applications and in the ships etc. STAMINA OF A GASKETED BOLTED FLANGED PIPE JOINT UNDER DYNAMIC LOADINGĭirectory of Open Access Journals (Sweden)įull Text Available Gasketed bolted flange joints are the most critical components in pipelines for their sealing and strength under operating conditions. Regardless of faying surface treatments, the first week charged at least 86% of total relaxation from this test. For 4.9 mil thick red lead painted treatment, the relaxation ratio was 18.7% for ASTM hexagon bolt, 34.9% for KS bolts. For ASTM hexagon bolt joints with a 5 mil thick zinc coating, the clamping force of the bolts decreased 15.0%, while relaxation ratio was 12.85% for KS bolts. In case of ASTM hexagon bolts, the initial clamping force dropped from 7.9% to 13.6% after 1, 000 hours while relaxation ratio was the range from 8.7% to 15.4% for KS bolts. Relaxation occurred for slip resistant joints with an uncoated surface that had been shot-blasted, cleaned, milled or rusted. The candidates for bolt were two kinds: Korean Standard and American Standard. Tests were conducted for slip critical joints subjected to various faying surface parameters. In case that special treatments are applied on a faying surface, the clamping force is relaxed severely. It is general that the clamping forces of high- strength bolts diminish within a certain time period after the initial clamping force. International Nuclear Information System (INIS) By using solid laminates, a new design for the joint zone is developed.Įvaluation of long-term relaxation for high- strength bolted connections
#Fasttrack schedule 10.0.1 crack full#
The studied joints have been used in a light full composite airplane. These s.This study represents an effort to predict the bearing strength, failure modes, and failure load of bolted joints in foam-core sandwich composites. By using solid laminates, a new design for the joint zone is developed.

This study represents an effort to predict the bearing strength, failure modes, and failure load of bolted joints in foam-core sandwich composites. Failure analysis of bolted joints in foam-core sandwich composites
